|
Custom Extrusions |
|
|
|
|
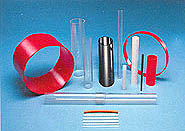 |
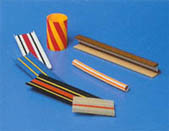 |
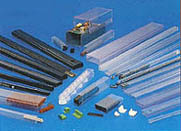 |
LECO PLASTICS was founded in 1946 with the goal of becoming a leader in the profile extrusion industry. Our commitment to continuous improvement, design innovation and process refinement has allowed LECO PLASTICS to be recognized as a premium custom supplier of plastic profile extrusions.
LECO PLASTICS specializes in tubes (round and square) up to 10" in diameter, co- extrusions; and non-laminated industrial profiles up to 14" in width. The materials extruded include: Rigid and/or Flexible PVC, Styrene, ABS, Polyethylene (low, medium and high density), Polypropylene, and some engineered thermoplastic resins such as Noryl and Alcryn. Secondary operations include: punching, bending, sonic welding, printing (silk screen, hot stamp, and inkjet), just to name a few, plus a special Antistatic dipping process for some of our electronic profiles applications.
Our Engineering department, along with our in-house Tooling (which features Wire EDM) and Quality Assurance Departments will work with our customers to design and develop applications specifications. This enables us to manufacture a tool capable of delivering a finished product that meets the customers requirements for fit and function, and interfaces easily with other mating parts.
Extrusion is a very involved process in which many variable conditions effect the process. It is important to keep in mind a couple rules of thumb. First, dimensions with tight tolerances are more easily achieved with rigid materials as opposed to flexible materials. Rigid PVC, Styrene or ABS are more forgiving than Polyethylene, Polypropylene or flexible Vinyl. Second, typically we need to keep a profiles wall thickness even throughout the design. Uneven wall thickness tends to create a problem in that the heavier areas take longer to cool and will result in excessive bowing. |
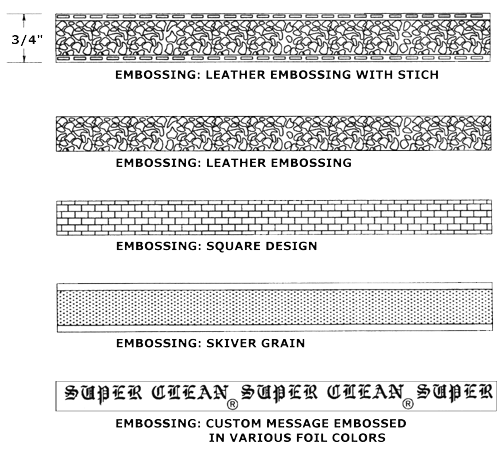 |
LECOPLASTICS extrusions with embossing have an added appearance. Choose from our embossings above or LECO PLASTICS can build a custom embossing for your product. |
 |
|
|